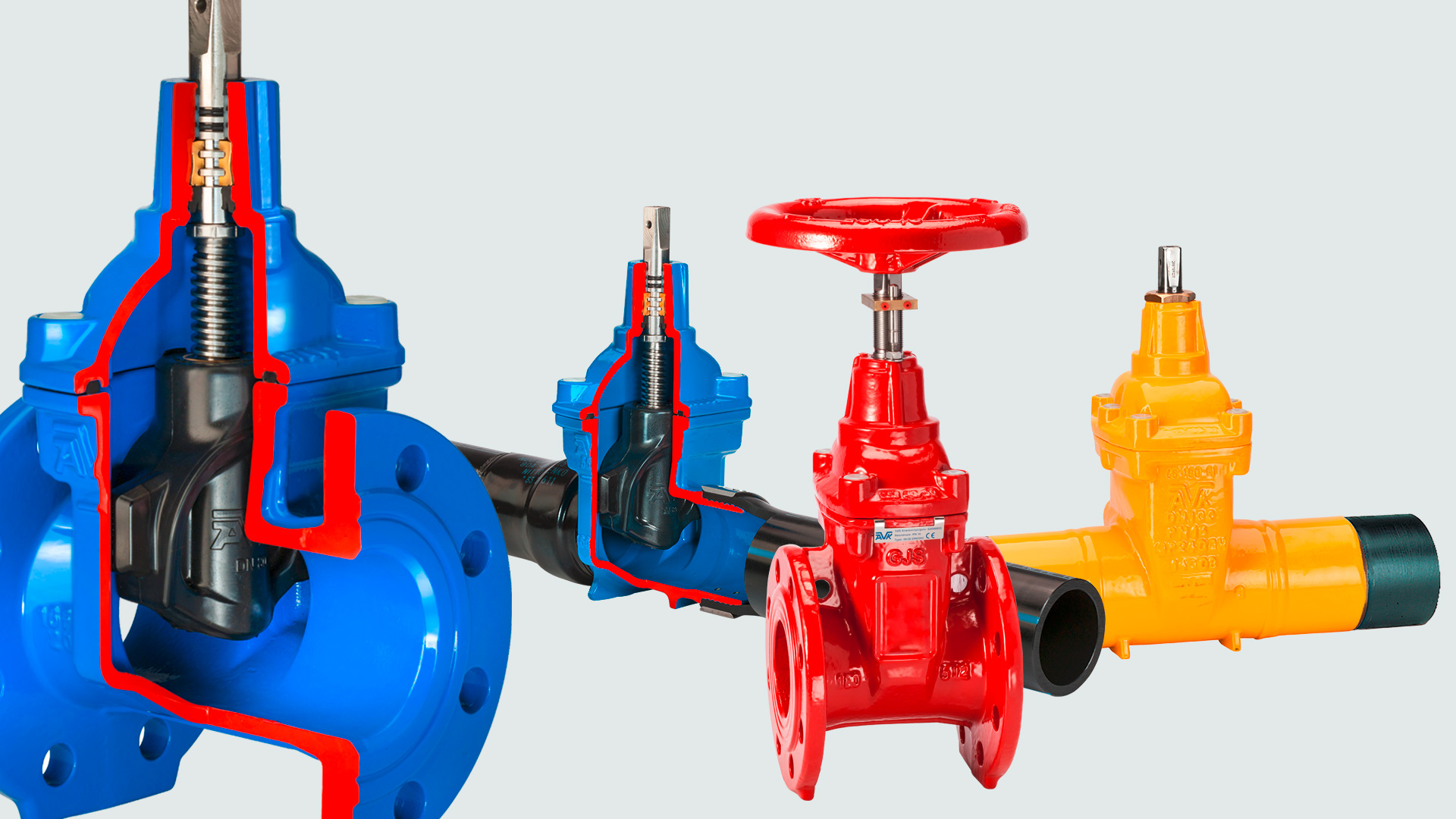
Gate Valves
Globalization has been made possible by AVK's commitment to quality and innovation. The gate valve line has been considerably expanded to satisfy local needs across the world. AVK provides Gate valves that comply with worldwide standards and come in various end connections and different material combinations. With more than 300 variants across AVK Group of companies.
The most common use of a Gate valve is when minimum pressure loss is required, and a free bore is a basic need. As long as a gate valve is fully open, there is no blockage in the flow channel. It shows minimum pressure loss, and its unique design makes pipe cleaning an easy job. As a multi-turn valve, a gate valve is operated through a threaded stem. To travel from open to closed, the valve must be rotated numerous times, which reduces the effect of the water hammer. These gate valves are effectively used for a long list of fluids. Following working scenarios support the AVK's gate valves:
- Potable water, wastewater and neutral liquids: temperature between -20 and +70 °C, maximum 5 m/s flow velocity and up to 16 bar differential pressure.
- Gas: temperature between -20 and +60 °C, maximum 20 m/s flow velocity and up to 16 bar differential pressure.
Design features of AVK gate valves
- Integral wedge nut is fixed and made of brass that is corrosion-resistant and is approved for use with drinking water.
- Wedge shoes are completely vulcanised to the wedge core for optimum corrosion prevention and smooth operations.
- Following are some more characteristics of AVK's wedge rubber:
- Little biofilm development
- Shape recovery abilities
- High level of chemical resistance while treating water
- Large stem hole in the wedge prevents stagnant water
- Wedge stop protects seals and coating
- Rolled threads increase the stem’s durability
- Triple safety stem sealing
- Thrust collar contributes to achieving low torques and secures the stem.
- The bonnet recess prevents blow-out as it has a fixed bonnet gasket that encircles the bonnet bolts.
- Countersunk bonnet bolts sealed with hot melt to protect against corrosion
- Full bore not only enables the use of pipe cleaning devices but also ensures low head loss.
- Easy operation is ensured by low operating torques.
- Epoxy coating in compliance with DIN 3476 part 1, EN 14901 and GSK, optionally internal enamel and external PUR coating